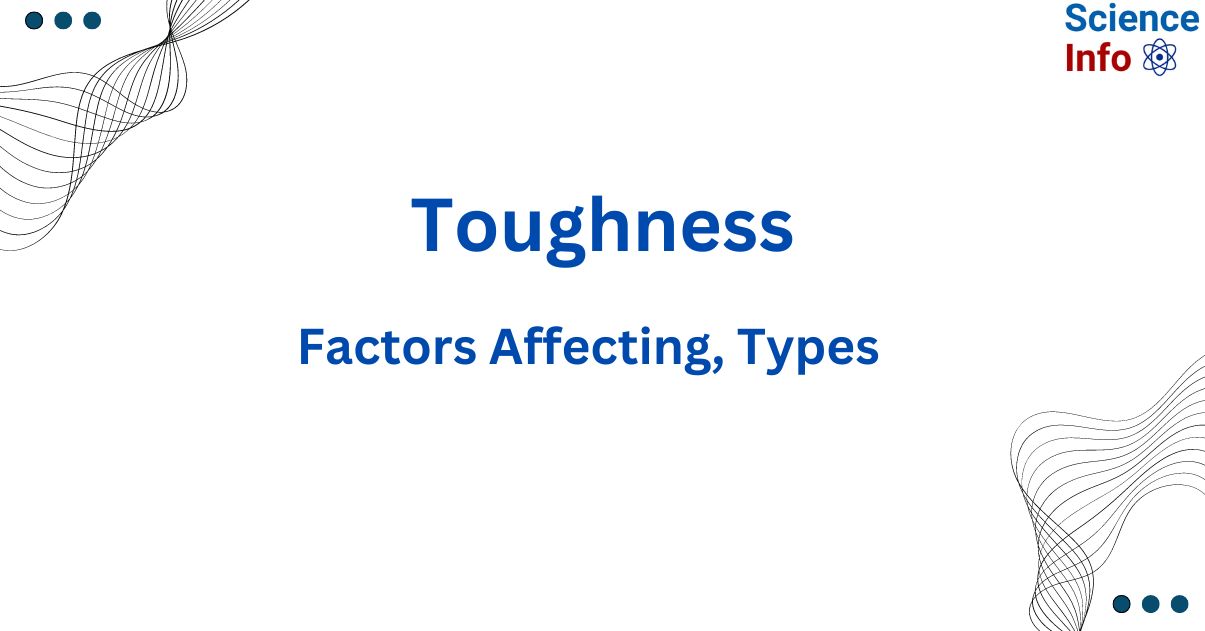
Toughness is a quality that allows a material to sustain impact loading without fracture. The harder material can withstand greater strain without breakage.
Toughness measures a material’s resistance to fracture while under stress. The energy required to break a substance is commonly measured in joules per cubic meter (J/m3). Materials with high toughness can absorb a great amount of energy before breaking and are frequently used in applications requiring impact resistance, such as building components or safety equipment.
It refers to how a material responds to unexpected impacts. It is the effort necessary to distort one cubic inch of metal until it cracks. The Charpy and Izod tests measure toughness.
Types of toughness
Two major types of toughness include:
Fracture toughness
Fracture toughness is a measure of the quantity of force necessary to propagate a preexisting fault. Flaws can occur as cracks, voids, metallurgical inclusions, weld flaws, design discontinuities, or a combination of these. Engineers often utilize the linear elastic fracture mechanics (LEFM) approach to design important components, assuming that a fault of a certain size will be present in some components due to the uncertainty of material quality.
Impact toughness
Charpy or Izod tests can assess a material’s impact toughness (or strength). These tests, named after their authors, were created in the early 1900s before fracture mechanics theory became available. Impact qualities are not directly employed in fracture mechanics calculations. However, cheap impact tests are still used as a quality control approach to measure notch sensitivity and compare engineering materials’ relative toughness.
Factors affecting toughness
Various variables heavily influence a material’s toughness. Some of them are:
Strain rate (rate of loading)
While a metal may be robust under static pressures, it may fail under dynamic loads or impacts. Ductility and toughness typically decline with higher loading rates.
Composition of material
The chemical composition of a substance can significantly affect its toughness. For example, adding specific constituents to a material, such as carbon in steel, can enhance its strength while decreasing its toughness.
Temperature
The temperature at which a material is loaded can influence its toughness. At high temperatures, a material’s toughness might diminish due to reduced strength and increased ductility.
Environment
The environment in which a material is utilized can influence its toughness. Exposure to corrosive conditions, high temperatures, and radiation may degrade a material’s toughness.
Material Processing process
A material’s toughness can be affected by its processing history, which includes casting, forging, and heat treatment. For example, certain heat treatments can improve a material’s toughness by improving its microstructure.
Notch toughness
The energy absorbed (impact energy) during the breakage of an object (with a fault, typically a V-notch) with standard dimensions and geometry under extremely fast (impact) loading is known as notch toughness. An imperfection, such as a notch or fracture, will most likely reduce a material’s toughness. This characteristic is measured using Charpy and Izod impact tests, which are useful for determining a material’s ductile-to-brittle transition behavior. Similarly to tensile toughness, notch toughness is measured in joules per cubic meter (Jm3) in the SI system.
Comparison between ductility and toughness
Ductility measures a material’s capacity to deform plastically (permanently) before fracture. It measures a material’s capacity to stretch or bend without breaking. Ductile materials can deform significantly before breaking, whereas brittle materials tend to break with minimal deformation.
Toughness, on the other hand, measures a material’s resistance to fracture while under stress.
So, ductility measures a material’s ability to flex, whereas toughness measures a material’s ability to withstand fracture under stress. Both qualities play a significant role in defining a material’s overall performance in a given application, and the best balance of ductility and toughness relies on the application’s specific needs.
The complex link between ductility and toughness is dependent on several variables, such as temperature, loading circumstances, and material type. In general, ductile materials are stronger because they can absorb more energy before breaking.
However, a material can have great ductility but poor toughness, or vice versa. Some metals, such as aluminum, are very ductile and strong, making them ideal for applications that require both qualities. On the other hand, some materials, such as cast iron, can be extremely brittle and break with little deformation, despite their high ductility.
Furthermore, temperature can affect the correlation between ductility and toughness. Examples of these changes in properties include ceramics, which become less ductile at high temperatures and more brittle at low ones, and elastomers, which become more ductile at high temperatures and less brittle at low ones.
Comparison between resilience and toughness
Toughness is the quality that allows the material to sustain impact loading without fracture. The ability of a substance to hold energy without permanent distortion is referred to as its resilience. Toughness and resilience are two characteristics of materials. Materials with resilience can retain energy without permanently deforming, and toughness allows them to sustain impact loading without breaking.
Strategies for Improving Toughness in Hard Materials
Microstructural Control
Adjusting the microstructure of a material may improve its toughness. Techniques include grain refining, management of phase distribution, and lowering the occurrence of defects lead to enhanced toughness. By lowering the density of flaws, the material becomes less prone to fracture and has greater toughness.
Composite Materials
Composite materials that have better fracture resistance and hardness can be made by combining hard components with tough matrix materials, including metals or polymers. By serving as a support structure, the hard matrix material inhibits the spread of cracks and increases the composite’s overall toughness.
Alloying
Adding modest amounts of ductile elements to a hard material can increase its toughness without appreciably reducing its hardness. For example, adding nickel to steel increases toughness while retaining a high hardness level.
Heat Treatment
In hard materials, appropriate heat treatment methods, such as tempering, can assist relieve internal tensions, lessen brittleness, and boost toughness. A material’s microstructure can be changed by heat treatment to increase its fracture resistance.
References
- https://www.imetllc.com/the-difference-between-strength-and-toughness
- https://efficientengineer.com/material-strength-ductility-toughness/
- https://www.engineersedge.com/material_science/toughness.htm
- https://uomustansiriyah.edu.iq/media/lectures/5/5_2018_03_11!09_55_46_PM.pdf
- https://www.researchgate.net/publication/291800541_Toughness_characterization_and_toughening_mechanisms
- https://www2.lbl.gov/ritchie/Library/PDF/Conflicts-nmat3115-Nov11.pdf